五軸機床對機床裝備制造業意義非凡,RTCP功能是衡量五軸機床性能的重要指標。在執行RTCP過程中,由于旋轉軸的加入,需要對直線軸進行非線性補償,因此旋轉軸和直線軸的伺服動態特性需要進行測定和調整,才能保證加工動態精度。本文對RTCP原理進行了簡單介紹,設計了一種五軸動態精度測定算法,通過該算法對五軸機床的5個伺服軸特性進行了強弱排序,從而對伺服參數進行優化和調整。以五軸葉輪加工為例,將伺服參數調整前后所加工的葉輪的加工質量進行對比,證明該方法取得了較好的效果。
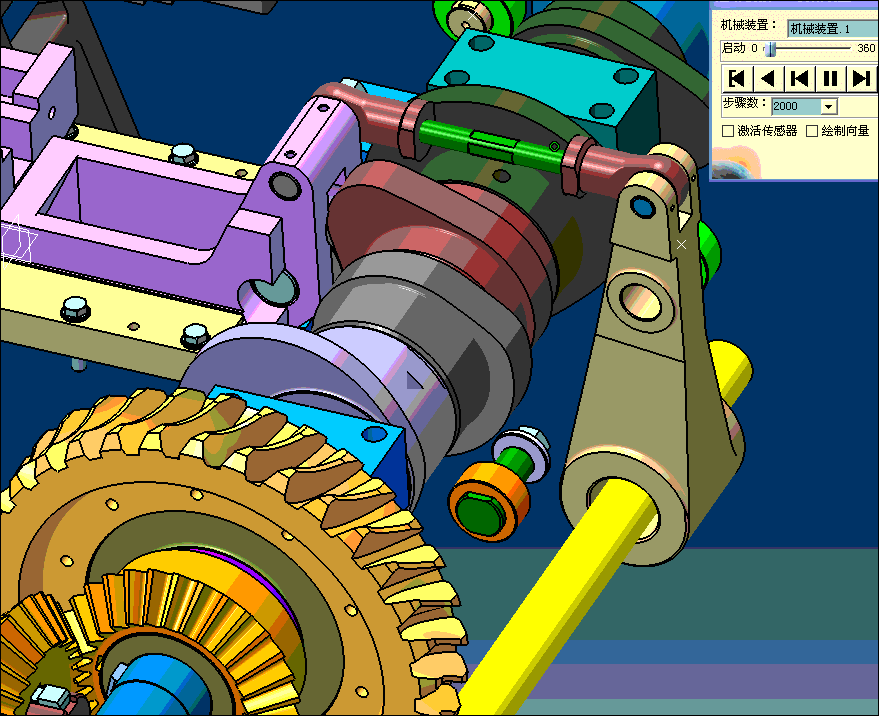
Abstract: Five-axismachine is significant for tool equipment manufacturing industry, and thefunction of RTCP is a very important reference to evaluate the performance of afive-axis machine tool. During the process with the RTCP function turning on,it needs a nonlinear position compensation for the linear axes because of therotary axes, so the ability of servo following of the linear axes and rotaryaxes is required to guarantee the processing dynamic precision. In this paper,the principle of RTCP is introduced and a kind of five-axis dynamic precisionmeasurement algorithm is designed. According to the algorithm ,the five axesare ordered, which helps to optimize and adjust the servo parameters . Takingfive axis impeller machining as an example, the machining quality of theimpellers is compared before and after the adjustment of the servoparameters, and it shows that the better results are obtained.
Keywords: RTCP;five-axis dynamic precision; servo dismatching degree
1.五軸數控機床比原有的三軸數控機床擁有更多優點,如加工復雜曲面、減少加工工序從而提高加工效率。但是由于旋轉軸的存在,在執行RTCP過程中,旋轉軸和直線軸會進行非線性運動,因此需要對五軸機床的動態特性進行控制,其動態精度成為影響加工精度的主要原因之一。五軸數控機床動態精度主要源于伺服系統加減速響應性能、零件受力變形、刀具振動、主軸轉速、機床進給大小等。按照常規的伺服匹配測定方法無法準確對直線軸和旋轉軸進匹配,五軸動態精度測定方法以RTCP功能特性為基礎,建立直線軸和旋轉軸聯動模型,通過測定后的結果為依據,來調整五軸數控機床的伺服參數,使伺服系統達到更好的狀態,從而提高五軸聯動數控機床的動態精度,提高機床的加工精度。
1. RTCP原理介紹
RTCP是Rotation Around Tool Center Point的英文縮寫,即圖1中刀具中心點編程。啟用RTCP,控制系統會自動計算并保持刀具中心始終在編程的XYZ位置上,刀具中心始終在編程坐標系中,轉動坐標每個運動都會被編程坐標系XYZ的直線位移所補償。使用RTCP,可以直接編程刀具中心的軌跡,而不用考慮五軸機床結構參數,大大簡化了五軸工藝編程和提高了加精度。
2.RTCP動態精度測定原理
在三坐標機床中,經常采用圓度測試來檢測任意直線軸間的動態特性是否匹配,但在五坐標機床運動過程中,由于旋轉軸的加入,必須在每個插補點對旋轉軸運動而帶來的直線軸偏差進行非線性補償,因此也必須對旋轉軸和直線軸間的動態特性進行伺服匹配。由于旋轉軸和直線軸的控制單位不一樣,不能像直線軸那樣直接采用圓度測試,采用本方法,可以對五個軸的動態特性進行測試和排序,從而為伺服參數調整提供依據。
以X、Y、Z直線軸加A、C轉臺軸的五軸機床為例,分析五軸之間的動態精度的調整方案。本測定方案之前,需保證X、Y、Z直線軸按照普通三軸機床調試策略進行了直線軸之間的匹配。
在RTCP運動過程中,A軸運動會引起Y、Z軸運動,C軸運動會引起X、Y軸運動。雖然加工過程中,五個軸會進行RTCP聯動,其動態精度測定過程也需要五個軸進行插補運動。但是由于建立五坐標RTCP動態測定模型比較困難,即使能夠建立模型,反映動態匹配的指標也不能夠直觀地引導進行伺服參數的調整,因此需要對兩個旋轉軸以及關聯的直線軸分別進行測定,簡化RTCP動態測定模型。本例中,A軸和Y、Z軸為一組測定,C軸和X、Y軸為另一組測定。由于Y軸與A軸和C軸都有關聯,在調試過程中Y軸伺服參數在一組測定完成后,另一組測定過程中不再進行調整。
以旋轉軸A為例,在RTCP生效時,A軸旋轉時,其關聯的Y、Z軸實際運動軌跡是以轉動半徑為圓心的圓弧。這里需要測定的內容包括:Y、Z直線軸之間的匹配和A、Y、Z旋轉軸和直線軸之間的匹配。具體測定過程如下:
(1)Y、Z直線軸之間的匹配
在旋轉路徑所在的象限中選取若干機床實際坐標采樣點,計算每個采樣點實際位置和指令位置之間的誤差值(圖2),根據每一象限誤差總和
和采樣點的個數,由下面計算公式得出不匹配值:
當計算結果:大于零,Y軸比Z軸強;小于零,Y軸比Z軸弱。對于C軸、X、Y軸的處理辦法和A軸、Y、Z軸是一樣的,以上測量過程就是常用的圓度測試方法。
(2)A、Y、Z旋轉軸和直線軸之間的匹配
在旋轉路徑所在的象限中選取若干機床實際坐標采樣點,通過Y、Z軸的實際位置可以計算出A軸最優位置圖3的值,A的實際位置由采樣得到,計算A軸的最優位置和實際位置之間的誤差值,根據誤差總和和采樣點的個數,由計算公式:/ 得到誤差平均值,就可以判斷直線軸和旋轉軸的強弱。C軸與X、Y軸的判斷方法和A軸的方法是一樣的。
根據上面測定方法,確定五個軸的強弱程度的排序,以此來進行伺服參數的調整。調整過程中,旋轉軸的伺服參數不進行調整,只調整直線軸的伺服參數。
五軸動態精度測定流程見圖4所示。
1. 功能測定及結果分析
為了測試算法的可行性,對葉輪加工做了對比實驗,實驗過程及結果如下:
3.1實驗裝置
1、DMG的AC雙轉臺五軸機床(圖5);
2、FANUC;
3、SSTT采樣軟件。
簡單介紹一下SSTT采樣軟件,SSTT是伺服調整工具(Servo Self Test Tools)的簡稱,主要用于配置FANUC數控系統的機床在線調試、診斷過程,也可以作為一種離線數據分析工具。本實驗主要通過SSTT工具采集各軸運動機床實際坐標數據,應用本文提出五軸動態精度測定方法來進行伺服參數調整,從而提高五軸RTCP動態特性。
3.2實驗方案
第一步,按照機床原定的伺服參數,加工葉輪的流道、大葉片及小葉片。
第二步,采用RTCP動態精度測試方法,計算直線軸與直線軸、旋轉軸與直線軸之間的不匹配度情況:
(1) 以A軸測試為例,在SSTT采樣軟件上設置好測試程序的相關參數,生成采樣程序并發送到下位機,測試程序如下:
%12345; A軸行程-90度到0度,開啟RTCP功能,實現A、Y、Z軸聯動;
G54 X-10 Y-20 Z-30 F2000
G01 A0
G128
M00
G01 A-90
M00
G01 A0
M30
機床運行該程序,由SSTT采集各軸的機床實際位置。當程序運行到G43.4 H1時,RTCP功能開啟,運行到第一個M00時,SSTT采樣開始,運行到第二個M00時,SSTT采樣結束。采樣過程中,以時域圖和圓軌跡圖顯示采樣情況,如圖6和圖7。
(2) 由采集的各軸的機床實際位置,用本文上述的RTCP動態精度測試方法,計算直線軸與直線軸、旋轉軸與直線軸之間的不匹配度。
第三步,通過計算結果來指導機床伺服參數(主要是軸的位置比例增益)調整,使其達到更佳的匹配狀態。如圖1所示,五軸RTCP功能最基本的原理是保證旋轉軸運動時刀具中心點保持不變,機床運動過程中使控制點繞著刀具中心點旋轉,其刀具中心點到控制點的距離稱為轉動半徑。由于雙轉臺類型結構的五軸機床,在實際加工中,刀位點是連續變化的,因此轉動半徑也是變化的,在動態精度測定前需要確定一個參考的轉動半徑作為測試樣本用例。在本次實驗中根據葉輪的加工區域選擇最大的轉動半徑作為測試用例,測定速度2000mm/min為實際葉輪加工的切削速度。測試中具體各軸調整情況如下:
(1)A軸
Y、Z、A軸伺服匹配見表1。
在進行A軸測定之前,由于旋轉軸和直線軸之間控制單位不一樣,需要先設定一個基準。在本實驗中,以旋轉軸為基準,盡量將A軸的位置比例增益調整到最優位置,該機床A軸位置比例增益調整到1300為上限,接下來做匹配時只需調整直線軸Y軸和Z軸的位置比例增益。以第三組實驗為例,計算過程如下:各象限的誤差總和及采樣點數分別為
考慮轉臺的旋轉方向矢量和G 代碼的指令方向,由計算公式1,計算出直線軸的伺服不匹配度為-1.525; 同理計算旋轉軸和直線軸之間的不匹配度為-0.947。
按照以上步驟計算A軸和C軸的各組實驗數據,比較實驗數據得實驗結果。
A軸測定條件下,匹配情況最好時,A軸、Y軸和Z軸的位置比例增益分別為:A1300,Z1283,Y1280。
(1)C軸
X、Y、C軸的伺服匹配見表2。
C軸測定條件下,匹配情況最好時,C軸、X軸和Y軸的位置比例增益分別為:C1280,X1280,Y1280。
第四步,調整參數后再次加工葉輪。
第五步,對比分析兩次加工的葉輪的質量狀況,從而分析算法的可靠性和可行性。
3.1實驗結果與分析
(1)調整前流道靠近小葉片頂端區域有明顯的過切痕跡,調整后過切痕跡
消失,表面光滑, 見圖8。
(1)調整前大葉片背面底部有明顯的過切痕跡,調整后過切痕跡消失,表面光滑,見圖9。
從實驗結果來看,經過五軸動態精度測定調整伺服參數后,葉輪中流道部分和葉片部分過切痕跡消失,加工表面質量有明顯改善,取得非常好的效果,說明該五軸動態精度測定方法有效,具有現場應用調試能力。
結語
本文提出的
五軸動態精度測定方法,通過現場應用調試,葉輪加工實驗對比,以及分析實驗結果可知,該方法確實能反映機床的動態精度,能夠指導提升機床的加工精度和表面光潔度。